Overall Equipment Effectiveness
Overall Equipment Effectiveness (OEE) is a key manufacturing metric that measures equipment productivity by evaluating availability, performance, and quality to identify losses and improve operational efficiency.
Understanding Overall Equipment Effectiveness (OEE)
In today’s highly competitive manufacturing landscape, efficiency and productivity are key factors in maintaining profitability and staying ahead of competitors. One of the most widely used metrics for assessing manufacturing efficiency is Overall Equipment Effectiveness (OEE). OEE is a powerful tool that provides insights into how well manufacturing equipment is utilized, identifying areas for improvement to enhance overall performance.
OEE measures three critical components of equipment productivity: Availability, Performance, and Quality. By analyzing these factors, manufacturers can identify losses, reduce waste, and improve production efficiency. This article provides an in-depth introduction to OEE, its calculation, benefits, and best practices for implementation.
The Three Pillars of OEE
OEE is calculated by multiplying three key metrics: Availability, Performance, and Quality. Each of these elements provides valuable insight into different aspects of equipment effectiveness.1. Availability
Availability measures the percentage of planned production time that equipment is available for operation. It accounts for unplanned downtime, such as machine breakdowns and equipment failures, as well as planned maintenance and setup time. The formula for Availability is:- Planned Production Time is the total scheduled production time.
- Operating Time is the actual time the machine was running, excluding downtime.
2. Performance
Performance assesses how efficiently a machine operates compared to its maximum potential speed. It considers factors such as slow cycles and minor stoppages. The formula for Performance is:- Ideal Cycle Time is the fastest possible time to produce one unit.
- Total Count is the number of units produced.
- Operating Time is the total time the machine was running.
3. Quality
Quality measures the percentage of good units produced compared to the total number of units. It considers defective products, rework, and scrap. The formula for Quality is:- Good Count is the number of units produced without defects.
- Total Count is the total number of units manufactured.
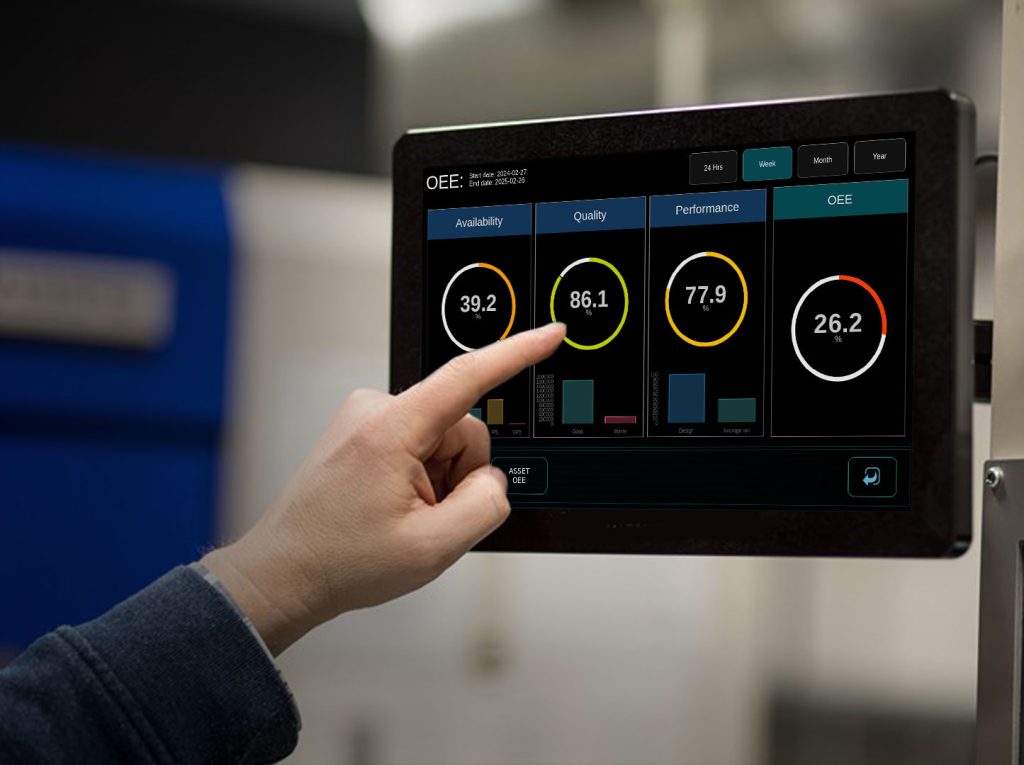
Real-time monitoring systems, such as, KDS’ Quantum Efficiency Management System, automatically track Overall Equipment Effectiveness on production machinery and can help manufacturers identify excessive consumption patterns and adjust their processes to optimize machine utilization.
Calculating OEE
Once Availability, Performance, and Quality are determined, OEE is calculated as follows:The Importance of OEE in Manufacturing
OEE is an essential metric for manufacturers because it helps identify inefficiencies, reduce waste, and improve productivity. Key benefits of implementing OEE include:
1.Identifying Losses
OEE highlights the six major losses in manufacturing:
- Equipment failure (unplanned downtime)
- Setup and adjustments
- Idling and minor stoppages
- Reduced speed operation
- Process defects
- Reduced yield
2. Reducing Downtime
By analyzing OEE data, manufacturers can pinpoint the root causes of downtime and implement preventive maintenance strategies to minimize equipment failures and unplanned stoppages.
3. Optimizing Production Efficiency
A high OEE score indicates that a plant is operating efficiently, producing high-quality products with minimal waste. Companies can use OEE insights to fine-tune production processes and maximize output.
4. Improving Product Quality
OEE helps track the number of defective products and identifies quality issues early in the production process. This leads to better quality control and reduced waste.
5. Enhancing Decision-Making
With accurate OEE data, manufacturers can make informed decisions about resource allocation, capacity planning, and process improvements.
Best Practices for Implementing OEE
To successfully implement OEE, manufacturers should follow these best practices:
1. Set Realistic OEE Goals
A world-class OEE score is around 85%, but most manufacturing plants initially score between 40-60%. Companies should set achievable improvement targets and gradually work toward higher efficiency.
2. Use Automated Data Collection
Manual data collection is prone to errors. Automated systems, such as IoT sensors and real-time monitoring software, improve accuracy and provide real-time insights.
3. Train Employees on OEE Principles
Educating employees about OEE and involving them in improvement initiatives fosters a culture of continuous improvement and enhances workforce engagement.
4. Implement Preventive Maintenance
Regular equipment maintenance reduces unexpected breakdowns and ensures machinery operates at peak performance.
5. Analyze and Act on Data
Simply measuring OEE is not enough. Manufacturers must analyze the data to identify bottlenecks and take corrective actions to optimize processes.
Conclusion
Overall Equipment Effectiveness (OEE) is a crucial metric for measuring and improving manufacturing efficiency. By assessing Availability, Performance, and Quality, manufacturers can identify areas for improvement, reduce downtime, and enhance overall productivity. Implementing OEE as part of a continuous improvement strategy enables organizations to maximize equipment utilization, reduce waste, and maintain a competitive edge in the industry. As manufacturing evolves with Industry 4.0 technologies, integrating OEE with real-time data collection and predictive analytics will further enhance operational efficiency, driving long-term success for manufacturers worldwide.Our Happy Customers
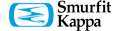
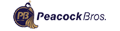
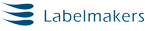
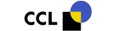
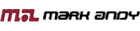
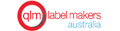
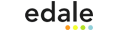
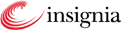
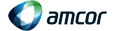
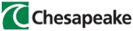
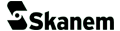