Machine Monitoring
Machine monitoring is the process of using sensors, software, and real-time data to track and optimize industrial equipment performance, reducing downtime, waste, and improving manufacturing efficiency.
Machine Monitoring:
Enhancing Manufacturing Efficiency by Reducing Downtime and Waste
Introduction
In modern manufacturing, efficiency is a key determinant of competitiveness and profitability. One of the most effective ways to enhance manufacturing efficiency is through machine monitoring—the process of using digital technologies to track, analyze, and optimize the performance of industrial machinery. This approach minimizes downtime, reduces waste, and improves overall equipment effectiveness (OEE), ultimately leading to higher productivity and cost savings.
Understanding Machine Monitoring
Machine monitoring involves the use of sensors, software, and connectivity solutions to collect real-time data from manufacturing equipment. This data is analyzed to provide insights into equipment health, performance trends, and potential failures before they occur. The technology often integrates with Efficiency Management Systems (EMS) and Manufacturing Execution Systems (MES) to facilitate seamless data analysis and decision-making.
By leveraging technologies such as the Industrial Internet of Things (IIoT), Artificial Intelligence (AI), and Big Data analytics, manufacturers can transition from traditional, reactive maintenance approaches to proactive and predictive maintenance strategies.
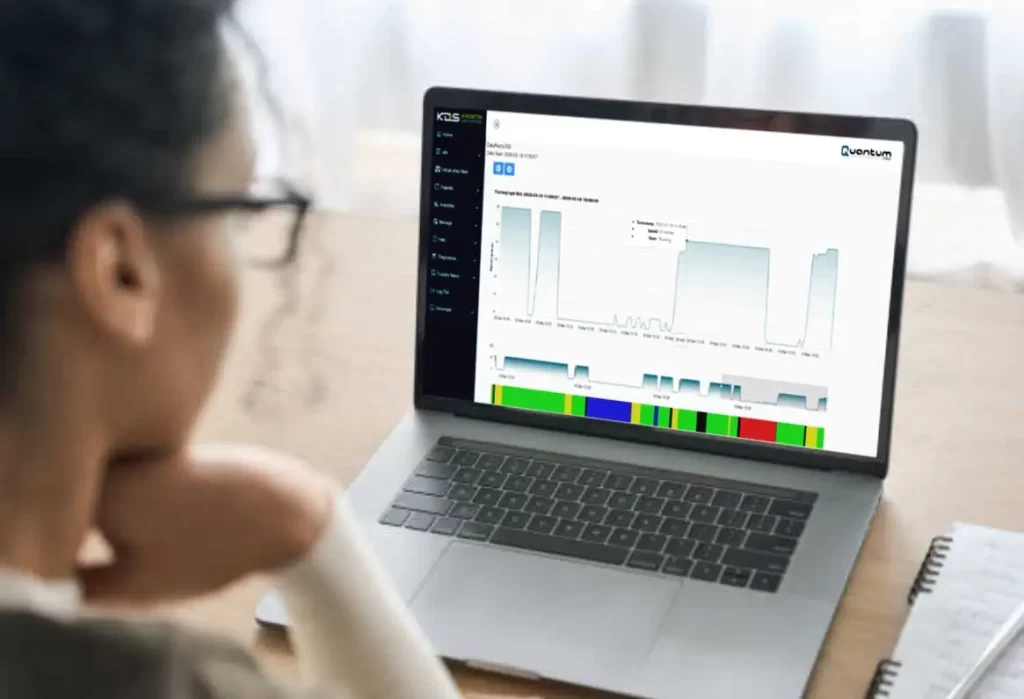
Real-time monitoring systems, such as, KDS’ Quantum Efficiency Management System, automatically track labor and substrate usage on production machinery and can help manufacturers identify excessive consumption patterns and adjust their processes to optimize machine utilization.
Reducing Downtime with Machine Monitoring
Downtime—whether planned or unplanned—remains one of the most significant productivity losses in manufacturing. Monitoring helps reduce downtime in the following ways:
- Predictive Maintenance:
- Sensors continuously track machine performance and detect early warning signs of failures (e.g., abnormal vibrations, temperature fluctuations, or motor inefficiencies).
- AI-driven analytics predict potential breakdowns, enabling timely maintenance before a failure occurs.
- Remote Monitoring & Alerts:
- Operators receive real-time alerts via dashboards, mobile apps, or emails when a machine exhibits abnormal behavior.
- This allows for immediate troubleshooting, reducing time spent diagnosing issues.
- Automated Scheduling:
- Monitoring systems optimize maintenance schedules based on actual machine usage rather than arbitrary time-based schedules.
- This minimizes unnecessary maintenance shutdowns and extends machine lifespan.
By implementing machine monitoring, manufacturers experience less unplanned downtime, increased asset utilization, and higher production efficiency.
Reducing Waste with Machine Monitoring
Waste in manufacturing arises from various factors, including material inefficiencies, production defects, and energy overuse. Monitoring plays a pivotal role in minimizing these inefficiencies:
- Quality Control & Defect Reduction:
- Real-time monitoring detects anomalies in production processes that can lead to defects.
- Automated adjustments ensure consistency in product quality, reducing scrap rates and rework costs.
- Material Optimization:
- Monitoring systems provide insights into raw material usage and highlight areas where material waste can be reduced.
- By tracking exact material consumption, manufacturers can make data-driven procurement decisions, minimizing overuse and stockpiling.
- Energy Efficiency:
- Smart sensors analyze power consumption patterns and identify excessive energy use.
- Companies can adjust operations to run machinery at optimal energy levels, leading to lower energy costs and reduced carbon footprint.
Andon boards are widely used in manufacturing to visualize daily production targets and display real-time production data. These boards provide operators and managers with instant insights into production performance, helping to identify issues and optimize efficiency. Key metrics from machine monitoring systems, such as equipment status, cycle times, downtime, and overall efficiency, are often integrated as live feeds into Andon boards. This real-time data enables quick decision-making, reduces response times to production disruptions, and enhances overall operational transparency.
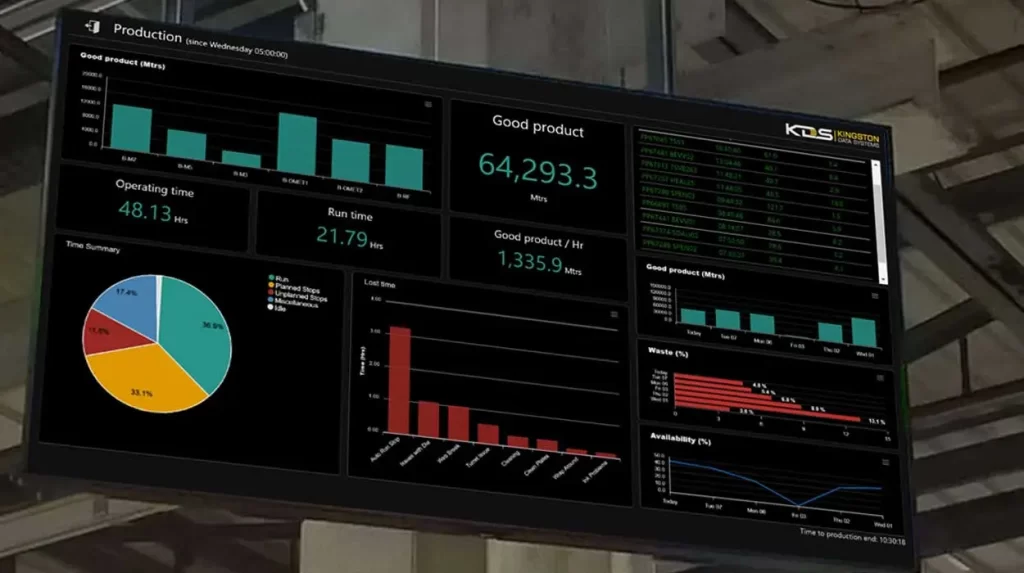
Improving Manufacturing Efficiency
Efficiency is the cornerstone of profitability in manufacturing, and equipment like KDS’ Quantum Efficiency Management System can contribute significantly to manufacturing efficiency. Machine monitoring contributes to lean manufacturing principles by ensuring machines operate at peak efficiency. Here’s how:
-
Optimized Production Planning:
-
Real-time data allows manufacturers to synchronize machine workloads, preventing bottlenecks.
-
Data-driven insights help adjust production schedules to maximize throughput while minimizing idle times.
-
-
OEE (Overall Equipment Effectiveness) Enhancement:
-
Machine monitoring directly impacts OEE, which measures availability, performance, and quality.
-
Continuous tracking and analysis ensure that equipment runs at optimal speed without sacrificing quality.
-
-
Workforce Productivity:
-
Automated monitoring reduces the need for manual checks, allowing employees to focus on higher-value tasks.
-
Operators receive actionable insights, leading to better decision-making and faster response times.
-
-
Integration with Efficiency Management Systems (EMS):
-
EMS tools aggregate data from multiple machines and provide centralized performance dashboards.
-
Managers can benchmark performance across different production lines, factories, or shifts, enabling continuous improvement initiatives.
-
Case Studies and Real-World Applications
Automotive Industry
Car manufacturers use IIoT-based machine monitoring to predict CNC machine failures in production lines. By doing so, they prevent costly downtime and maintain a just-in-time manufacturing approach.
Food & Beverage Industry
Monitoring equipment such as mixers and packaging machines ensures consistent production speeds and minimizes material waste, improving both quality and profitability.
Aerospace Manufacturing
Aerospace companies integrate machine monitoring with MES to track every stage of production, ensuring compliance with strict quality standards while reducing defects.
Future of Machine Monitoring
The future of machine monitoring is driven by advancements in AI, cloud computing, and edge analytics. Some key trends include:
-
AI-Powered Predictive Analytics: Machines will become even more autonomous, self-diagnosing potential faults before they escalate.
-
5G-Enabled Connectivity: Faster data transmission will enable real-time monitoring on a massive scale.
-
Cybersecurity Enhancements: With increased connectivity, secure data transmission will be paramount to prevent cyber threats in industrial settings.
Conclusion
Machine monitoring is revolutionizing manufacturing by reducing downtime, minimizing waste, and enhancing efficiency. By leveraging IIoT, predictive analytics, and efficiency management systems, manufacturers can maximize productivity while cutting costs. Investing in monitoring technology is no longer a luxury—it’s a necessity for businesses striving to remain competitive in today’s fast-paced industrial landscape.
References
-
Lee, J., Bagheri, B., & Kao, H. A. (2015). “A Cyber-Physical Systems Architecture for Industry 4.0-Based Manufacturing Systems.” Manufacturing Letters, 3(1), 18-23.
-
Rojas, J., & Wang, L. (2019). “Machine Learning in Manufacturing: Advantages, Challenges, and Applications.” Journal of Manufacturing Science and Engineering, 141(5), 051014.
-
Industry Week. (2023). “How Machine Monitoring Reduces Downtime and Enhances OEE.” Retrieved from industryweek.com
By implementing machine monitoring solutions, manufacturers not only enhance operational efficiency but also gain a significant competitive edge in an increasingly digital-driven industrial environment.
Our Happy Customers
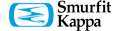
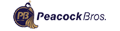
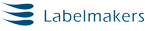
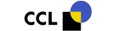
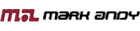
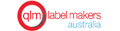
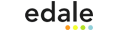
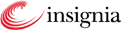
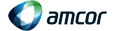
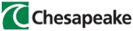
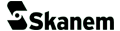